A Laymans Guide To Concrete Moisture and Floor Covering
By Chuck Brewer
As most of you know, concrete is a mixture of aggregates, cement and water. As the concrete cures, moisture moves to the surface through capillary action. This process continues for the life of the concrete.
Even when the concrete is "dry" it contains moisture. The moisture content varies due to quite a few factors. Here’s the big ones:
1. The original concrete mix.
2. The porosity of the concrete.
3. The thickness of the slab.
4. A synthetic vapor barrier (or lack of) beneath the substrate.
5. Intrusion from outside influences like irrigation systems and/or water runoff from landscaping.
So how does this effect flooring? Yesterday’s asbestos and solvent based adhesives have been replaced by today’s “eco-friendlier” latex based ones. The prior adhesives were inherently resistant to liquid moisture (think oil and water). Latex itself is water based and can actually draw moisture from concrete. Today’s flooring adhesives, when exposed to high moisture levels in concrete, don’t cure properly and provide the bond required.
What types of flooring are affected by concrete moisture? Almost all commercial products with the possible exception of “action back” (latex mesh-backed) broadloom carpet. Of course the materials vary in their reaction to moisture. Here are examples from most sensitive products to least:
1. Heat-welded resilient sheet or linoleum.
2. Sheet rubber. 3. Cork sheet or tile.
4. “Vinyl back” broadloom carpet (typically 6’ wide).
5. Modular carpet.
6. Luxury vinyl tile and plank.
7. Hardwood flooring.
8. VCT (vinyl composition tile).
There’s more but you get the idea. Prior to flooring installation the slab should be tested to see what the moisture content or “concrete dryness” level is, right? Believe it or not, some contractors skip this vital step. Why?
1. The existing flooring is fine and doesn’t show any signs of a moisture problem.
2. The testing is too expensive based on the size of the job.
3. “I’ve been installing flooring for 30 years and never had a problem”.
4. If the test results come back “high” there will be a battle between client and contractor to assign fault and determine who’s financially responsible for “the fix“. Let’s assume the voice of reason chimed in and the decision is made to test.
What kind of testing is used? For commercial carpet and resilient flooring two methods are typically used:
1. The CaCl2 (Calcium Chloride) method which measures emission (MVER) in lbs. per square foot. A reading under 3 lbs. is acceptable for most resilient flooring, a reading under 5 lbs. is acceptable for most carpet.
2. In-situ relative humidity testing (RH). This system measures moisture content in percentages. For example, a reading under 75% is acceptable for most flooring, under 85% for some carpet.
Which method is the more accurate, or the more reliable? Most floor covering manufacturers recognize one or the other (sometimes both) in relation to warranties. The flooring industry is moving more toward RH testing because it measures concrete moisture deeper into the substrate and is less affected my external (or ambient) conditions.
One more thing, There are very strict testing standards put out by the American Society for Testing and Materials. ASTM.org. (F1869 for Calcium Chloride), (F2170 for Relative Humidity). These standards cover proper testing methods, locations, quantities and job-site conditions. If the testing does not comply with ASTM standards the test results are null and void.
So, we’ve gone by the book, done proper testing and the results are not in compliance with the manufacturer’s requirements. Don’t be surprised. Most concrete slabs don’t comply. Why? Probably too much water.
1. A wetter mix makes the concrete easier to place.
2. Water added to the surface of the slab aids in the finishing and curing process.
3. Water is added so the material can be pumped to elevated decks.
4. Lack of (or a damaged) vapor barrier.
5. Water intrusion from irrigation or ground slope.
OK the concrete moisture level is too high, what are the options? Here they are listed by worst idea to best:
1. Ignore the results, install the floor and hope for the best.
2. Apply the least expensive “concrete sealer“ available and roll the dice.
3. Contact the manufacturer for their recommendation of an approved moisture resistant adhesive.
4. Mechanically scarify the slab and apply a proven and warranted vapor control system.
Obviously options #3 and #4 make the most sense. Let's look at some budget numbers. Here’s some good news. Manufacturer approved moisture resistant adhesives can cost as little as $.50 to $1.00 per sq. ft. If there are no special adhesives available for the specified product (often times they are not) the option may be #4. OK, what’s that going to cost? Anywhere from $3.00 to $5.00 per sq. ft. depending on the size of the area. Seem like a lot of money? …Not really…Think of a couple of things:
1. The life-cycle cost per the life of the flooring material (typically 10 years minimum). Your average cost to protect/insure your expensive floor covering is approximately .40 to .50 cents per sq. ft.
2. Replacement cost of your flooring if and when a failure occurs. This varies depending on the flooring and the application but take into consideration these factors: removal and replacement of furniture, computers, etc., add demo of the flooring and adhesive, installing a vapor control system (we didn’t the first time), then add material and labor costs for new flooring. All this work will probably be phased/after hours (at an additional cost) to create minimal chaos and keep the business operating. It’s safe to say that this could easily cost 4 to 5 times the original price.
Ready for some more good news? Architects, design professionals, construction managers and contractors “in the know” pre-budget concrete vapor emission solutions into the project pricing. Typically floor covering is pretty far down the list cost-wise on a project. By accounting for additional cost up front, the impact is minimal and there are no surprises or delays to the project. These are contingency costs. If a concrete moisture control system is not needed, the money goes back to the owner! I stated earlier that most slabs don’t comply with manufacturer requirements, how does that save money? Easy. Flooring options are available in every category and for every application. Many have higher moisture tolerances, special backing systems, installation methods or moisture resistant adhesives.
That’s where we can help. We work with design people, construction managers, contractors and end-users to review products, inspect job sites, test substrates and find solutions. We are experts in value-engineering to keep costs down while still maintaining the integrity of the project. We are an independent consulting service, not affiliated with manufactures, vendors or agents. Please contact us if we can be of further assistance, answer questions or address concerns.
About the Author
|
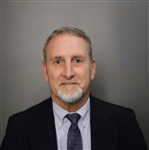 | Chuck Brewer, Brewer Contract Consulting 5416 Lodi Street San Diego, CA 92117 858-999-5807
Contact Author: request info
If you would like to re-print this article, please contact the author.
|
|
|
|
|